KOSUN must do anything to enable the clients to get more benefits and to seek more business opportunities in the market. We promise to create more values for you and the society.We must develop new technologies and new products for our clients, and make our popularity on a high level in this field.We must heighten our position and set a good example in this field. A group of experienced staff are ready to serve our clients with enthusiasm at any time!
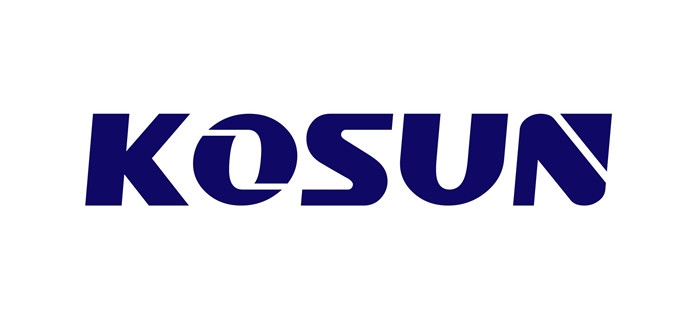
Service concept: It is all about the clients,and provide clients with high value-added products.
Service orientation:
Regard the realization of service promise as the destination; implement the concept of high-quality,high-taste, high-efficiency and all-around-way service in the process from the design, manufacturing,management to the sale of products.
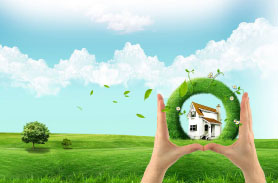
Service promise:From the design, we will do every step carefully to maximize clients satisfaction.
1.Pre-sale service: Act as a good adviser and assistant of clients; enable them to get rich and generous returns on their investments.
(1) Select equipment model;
(2) Design and manufacture products according to clients’ special requirement;
(3) Train technical personnel for clients;
2.Service during the sale: Respect clients; devote ourselves to improving the total value of clients. (1) Pre-check and accept products ahead of delivery; (2) Help clients to draft solving plans.
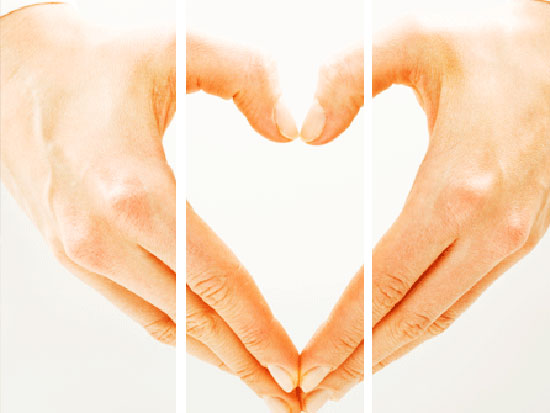
3.After-sale service: Provide considerate services to minimize clients’ worries.
(1) Assist clients to prepare for the first construction scheme;
(2) Install and debug the equipment;
(3) Train the first-line operators on site;
(4) Examine the equipment regularly;
(5) Take initiative to eliminate the troubles rapidly at site;
(6) Distribute the guarantee fittings door-to-door;
(7) Provide perfect service;
(8) Provide technical exchanging;
(9) Provide maintenance for big items.