In China oil drilling fluids solids control industry, KOSUN is a pioneer and leader, we has been providing solids control equipment for more than 20 years, the products include shale shaker, shale shaker screen, desander, desilter, vacuum degasser, centrifugal pump, submersible slurry pump, shear pump, mud agitator, mud gun, drilling fluids mud cleaner, decanter centrifuge, jet mud mixer, mud tank, diesel tank, water tank and complete solids control system, etc.
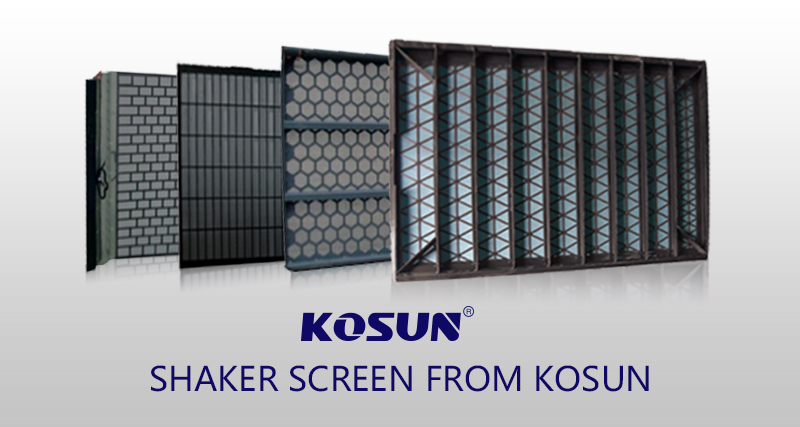
Shale Shaker Screen is main spare parts for shale shaker. Shale Shaker Screens are easy to be broken during the shaker operation when drilling well.
Drilling fluids shale shaker is a kind of filterable mechanical separation equipment, compared with other mechanical solids control equipment, its unit cost is kinda of economic. And it is a highly efficient separation equipment which obtains solid removal amount. Drilling fluids shale shaker is made of screen body, machine rack and gearing. Accordingly, mechanical vibration will make solid phase which is bigger than screen hole and the adhesive attraction will screen the solid phase particles which is smaller than screen hole. But all mud can’t be processed in circulating process because of the limit of shale shaker mud permit.
Usually the material of drilling fluids shale shaker is stainless knitted. Usually this kind of screen uses mesh to express the specification. Mesh is the number of screen holes, for example, a square screen that has 12 holes is called 12-mesh screen. Screen with a special outfit screen holder will screen into flake tension type fixed on the screen frame. Screen body is fixed to the rack based on spiral spring, and rubber articles’ bumper adopts the bottom-fixed type.
The Parts of the Shale Shaker Screen Panel
Oil Rig Shaker Screen Frame-Much like a canvas for painting a screen has to be supported on a frame in order to do its job, this frame differs between manufacturers in both material and shape. Screen frames can be made from materials, such as, square steel tubing, flat steel sheets, plastic type composites or they can just be supported on the ends with strips of steel ( similar idea to a scroll ). These frames consist of a rectangular shaped outer perimeter which is divided into small individual inner panels. These smaller panels differ in shape from manufacturer to manufacturer and have been known to come in shapes such as square, hexagonal, rectangular and even triangular.
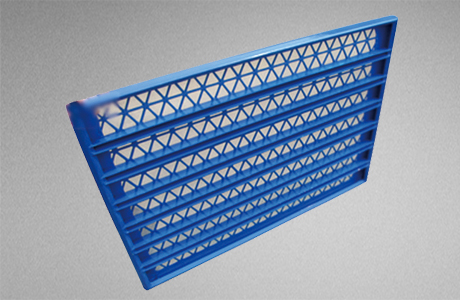
These differing panel shapes are used in an attempt to reduce the quantity of panels on each frame but still provide maximum rigidity and support for the mesh attached to them. The purpose of reducing these panels is to maximize usable screening area as the walls of each panel get in the way of the mesh and prevent it from being used, this is known as “blanking”. The non-blanked screening area of a shaker screen is widely used as a selling point, the more screen surface you have available to work, the more efficient your shaker becomes and therefore can handle a higher quantity of fluid.
Screen Mesh-Just like thread is woven together to create cloth, metal wire can be woven to create a metal cloth. Screen Mesh has evolved over many years of competitive screen manufacturing resulting in very thin yet strong cloth designed to maximize screen life and conductance as well as to provide a consistent cut point. To increase the conductance of a mesh screen you have to minimize the amount of material in the way, this is done by either reducing the wire diameter or weaving the cloth to produce rectangular openings. Rectangular openings increase the screens conductance while minimizing the effect on its cut point where as square openings provide a more consistent cut point but offer a lower conductance.
To maximize screen life most manufacturers build their screens with multiple layers of mesh over a very sturdy backing cloth to further protect the cloth against solids loading and wear. The multiple layers of mesh act as a de-blinding mechanism pushing near sized particles, which may get stuck in the openings, out of the mesh reducing blinding issues and keeping the screen surface available for use.
Binding Agent-The binding agent is the material used to bind the mesh to the screen frame, it is designed to maximize adhesion to both materials while being able to handle high heat, strong vibration, abrasive cuttings and corrosive drilling fluids.
Plastic composite screens tend not to use adhesives but rather heat the mesh and melt it into the screen frame to form a bond.
3D Screen Technology-One of the more recent advances in oilfield screen technology has brought us the “3D screen”, this technology is an innovative method for increasing the screening area of a shale shaker without the need to build larger machines. When seen from the side, these screens look like corrugated cardboard, having a flat bottom and wavelike shapes on top. These waves are designed to increase the surface area of the screen panel by building up instead of out, thereby maximizing the surface area of the screen without the need to build larger shaker screens and in turn larger, heavier and more expensive shakers.