Shale vibrating screens play a vital role in the oil drilling industry, especially in the process of separating drilling mud from drill cuttings. These devices utilize a variety of vibrating screens, including linear vibrating screens and elliptical dual-track vibrating screens, to effectively remove solids from drilling fluids. Using vibrating screens not only helps maintain drilling mud properties but also reduces the environmental impact of drilling operations.
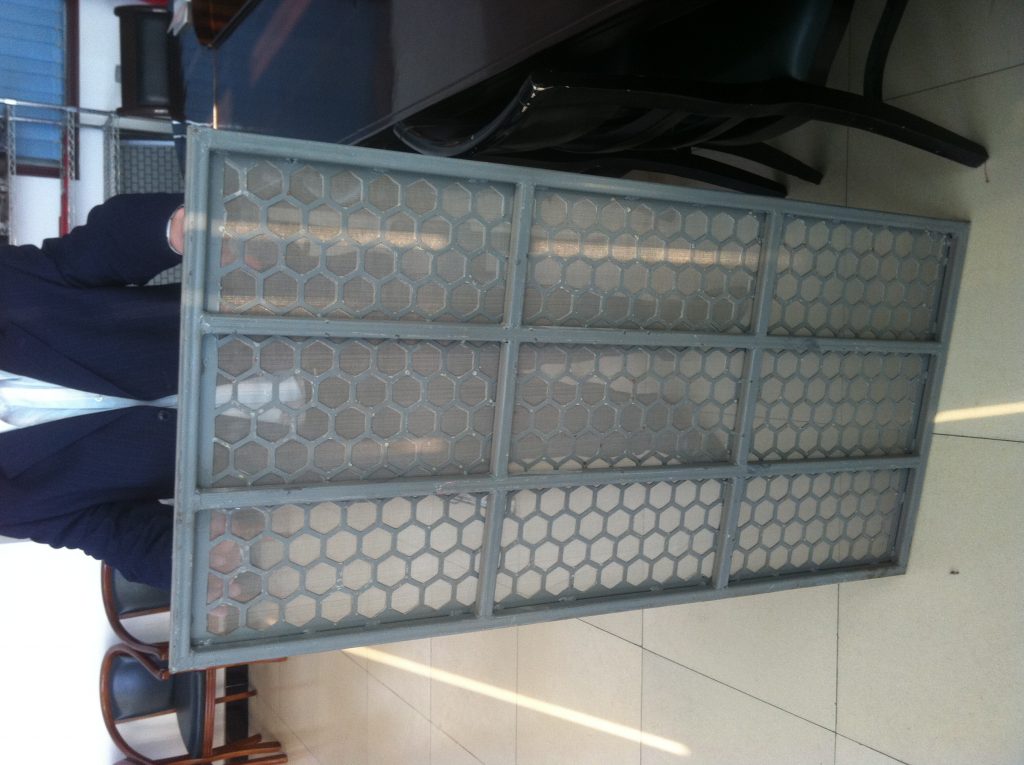
Linear vibrating screens are often used in vibrating screens to effectively separate solid particles in drilling mud. These screens use linear motion to move drilling mud across the screen surface, allowing smaller particles to pass through while retaining larger particles. This process ensures that the drilling mud is free of debris, which is critical to the overall success of the drilling operation.
In addition to the linear vibrating screen, an elliptical double-track vibrating screen is also used in the vibrating screen to improve the efficiency of the separation process. These vibrating screens feature a dual-motion mechanism that combines linear and elliptical motion to effectively remove solids from drilling mud. Using an elliptical dual-track vibrating screen allows for more complete separation of cuttings, resulting in cleaner drilling mud and improved overall performance.
In addition, mud drying shakers and drilling fluid shakers are integral components of shale shakers and help improve the overall effectiveness of the solids control process. These screens and shakers are used in conjunction with linear shakers and elliptical twin-track shakers to ensure that drilling mud is properly processed and ready for reuse in drilling operations.
Overall, the use of various vibrating screens and vibrating screens in shale vibrating screens, such as linear mud vibrating screens and elliptical dual-track vibrating screens, is crucial for effective separation of solids from drilling mud. This process not only helps maintain the integrity of the drilling fluid but also minimizes the environmental impact of oil drilling operations. As the oil drilling industry continues to evolve, the importance of shale shakers and their associated shakers and shakers in ensuring the success and sustainability of drilling operations cannot be overstated.