Shaker Screen
Shaker Screen consists of a frame that can either be of steel or plastic, into which mesh can be fitted. This mesh does the work of separating the mixture of solid and drilling fluid. A binding material is used to bind the mesh with the frame.
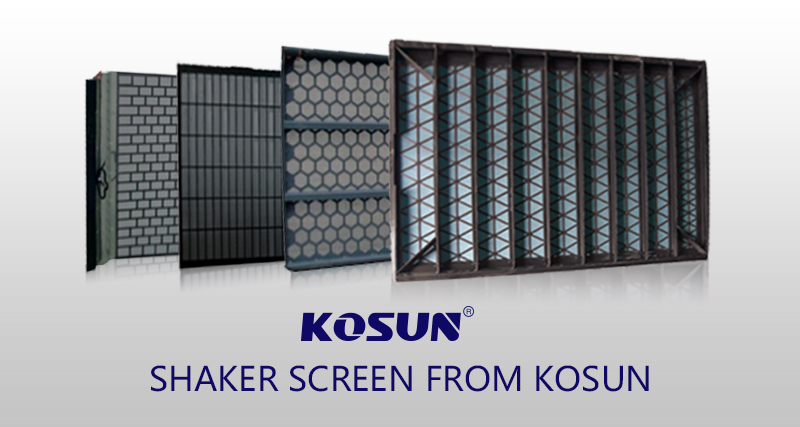
For maximum efficiency, Shaker Screen must be used properly. Following points describe how to properly use it.
– The cloth that is used for making the mesh must be of good quality. Also, if the layering of the mesh is increased, the efficiency of the screen will automatically increase and the fineness of the mesh will also increase.
– Methods must be implemented to increase the life of the screen. For this the first method is to have a very strong screen so that the meshes are supported very firmly. The second method is to provide proper tensioning to the screen.
– The screen must be protected from over tensioning or under tensioning.
– When not in use, the screens must be properly removed from the machine, cleaned and stored properly. Extra care must be taken while storing the screen.
– Also, when the screen in being installed, care must be taken that they are not mishandled. Mishandling of the screen, especially during installation may cause extra wear and tear.
– The weight of the mixture that is being fed to the screen must be in accordance to the amount of weight that the screen can handle. Different types of screens are available for various sizes of the mixture.
– The screens must be cleaned frequently and carefully. Care that must be taken during cleaning the screen is, the water that is being used is not of very high pressure or else it may cause the mesh to unbind from the frame.
KOSUN will supply better goods and services to customers continually.